Manufacturing
Head of Operations
Goal: Supervise, Lead, motivate, direct, develop and innovate on a team of production employees. using innovative AI.
Head of Engineering
Goal: Inspire engineers to use and layout product design, yield and cycle time using AI.
Chief Digital Officer
Goal: Take up digital initiatives matching the strategic-planning process, using AI with leadership commitment.
Chief Innovation Officer
Goal: Developing, strategizing, and planning new AI based processes that will drive innovation, cost reduction and reduced Carbon.
The manufacturing Industry has always taken the lead in innovation and Digital Transformation. The Fourth Industrial Revolution is upon us and Oceans.ai is taking the lead.
Volume and efficiency used to be the key SLAs in this industry. It is clear that today, these SLAs have grown in both size and complexity. The Industry 4.0 demands better data collection, smarter processing, and deeper insight. Always based on multi-device data collection.
Modern manufacturing already has advanced technology like control systems, robots and fully-automated assembly production lines. Various systems control these production lines.
With industries adding further technologies like additive manufacturing, autonomy of robots, AR/VR for remote asset monitoring and lot bandwidth connectivity for IoT, things get more complex in a plant environment. But all these various systems must provide the customer with an integrated and unified view of the asset to make business-critical decisions.
Oceans.ai’s systems and solutions boost the Industry 4.0 innovation processes, Some use-case scenarios:
- Plants are shut down for 1-2 months per year to enable planned inspections and maintenance, creating downtime.
- If this downtime can be reduced by even 10-20%, it will make a pivotal difference
- Efficient asset inspections, including remote assets, are preventative measures that will significantly reduce downtime, operational and profit losses.
- In toxic environments, instead of shutdown and wait periods (to remove toxicity), plants can use robots to perform regular plant inspections remotely.
Intelligent Robotic Remote Plant Inspections (Scheduled and Unscheduled)
- This, along with IoT sensors, plant gauges and control system data, will give remote operations and AI-powered systems sufficient intelligence to make decisions related to shutdown inspection.
- Stray mixing of raw materials (including water) in chemical plants across units can be catastrophic. By combining visual, thermal, and sensor-based data, our solutions can prevent or reduce risk.
Optimised Plant Monitoring
- This is achieved through a mix of in-asset sensors, context-aware on-robot sensors, plant gauge readings and control system data.
- Today manufacturing is powered by various systems and processes, both connected and disconnected.
- Seamless integration between systems and processes by making meaningful interpretations and corroborations with available data
- Having all IoT sensors across plant assets can be costly for monitoring – this is where our solution, which combines on-asset sensors with on-robot sensors, can optimise sensor deployment across the plant.
Plant Simulation and Predictive Planning
- Sensors attached to plant assets, or through regular robotic inspections, will transmit data to the digital twin, providing the manufacturer with critical information about the plants’ performance. This information can be used to conduct simulations and predict issues.
Safer Environments
- Work safety and compliance and manufacturing environment monitoring can significantly reduce human costs and human-led error in manufacturing environments.
- Oceans.ai enables manufacturers to monitor worker activity, machinery compliance, and causes of safety shutdowns in real time. We use industrial IoT data among other datasets. Employees can wear smart devices to track biometrics like body temperature, allowing supervisors to oversee health concerns.
- Finally, machine learning can enable video and robotic surveillance systems to detect when workers are not wearing proper protective equipment or engaged in unsafe practices. Paired with sensors on the shop floor and robotic inspection data, machine learning can also provide insight into the performance of safety systems to identify root causes of shutdowns and identify leading indicators of machinery issues.
Predictive Maintenance
Predictive Maintenance (PdM) leverages real-time data to promptly identify core issues in the manufacturing process and take necessary corrective actions. It helps to analyse data by studying the difference in nature and frequency and alerts the system to reduce the potential risks of failure. PdM guides the manufacturing industries in optimising top-notch quality products at a lower cost.
PdM systems can also help companies predict what replacement parts will be needed. Using machine learning for predictive maintenance allows manufacturers to foresee when equipment failure is likely, to enable proactive part replacement or repairs.
Manufacturing: Chemical Plants, Petrochemical Plants, Offshore and Onshore refineries
- Automated quality testing can be realised using AI. By employing advanced image recognition techniques for visual inspection and fault detection, productivity increases of up to 50% are possible.
- Collaborative robots are particularly relevant concerning tasks that are not fully automatable. In such settings, they hold the potential of increasing productivity by up to 20%.
- “ Inspection costs may be reduced by up to 25%, and an overall reduction of up to 10% of annual maintenance costs is possible. “
Reduce Complexity
Reduce the complexity of plant inspection by having all inspection information in a single repository with visually context-able and corroborate-able data with interactive reports. Track progressive inspections of varied natures, at various times or simultaneously, across different platforms, eradicating document-based inspections.
Corroborate data
Be able to link asset condition findings across related and connected assets easily. Corroborate data across inspection and asset conditions to make smarter predictive and preventive maintenance decisions.
Build Smart AI
Use our continuous AI learning engine and the expert-in-control approach to build smart and meshed AI that can integrate with robotics and drone-based systems to reduce plant downtime and improve the accuracy of plant inspections over time. Additionally, minimise workforce exposure to risky plant environments (like chemical plant units).
Testimonials

“Lorem. The easiest and most accurate way to track time across teams and finish the projects. Timely’s automatic.”
Wade Warren
CTO, Waverio

“Lorem. The easiest and most accurate way to track time across teams and finish the projects. Timely’s automatic.”
Jenny Wilson
President of Marketing, SS

“Lorem. The easiest and most accurate way to track time across teams and finish the projects. Timely’s automatic.”
Marvin McKinney
Founder, Creaty
Contact us today for a Demo
We can help you assess different strategies to reduce costs, improve productivity and become more impactful on the environment.
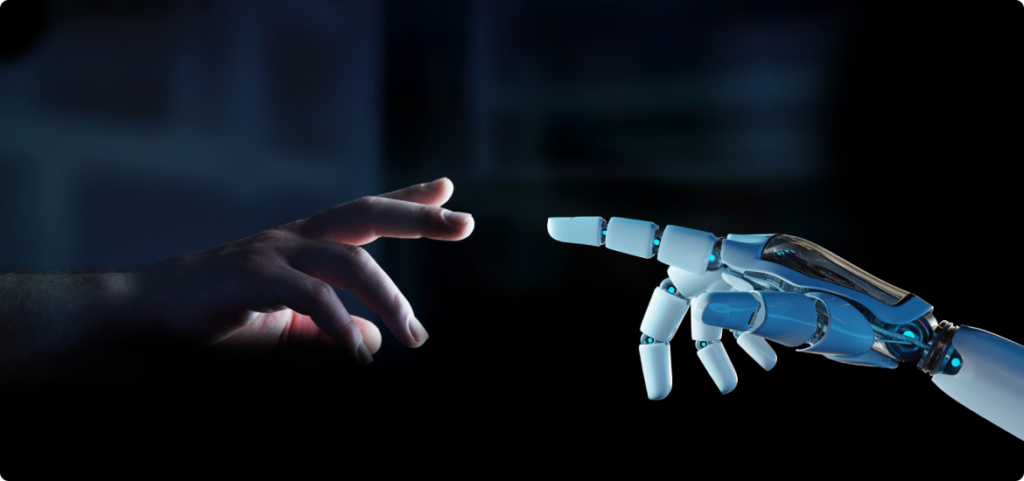
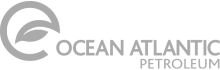

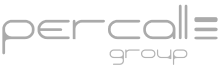
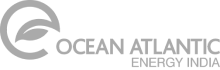
